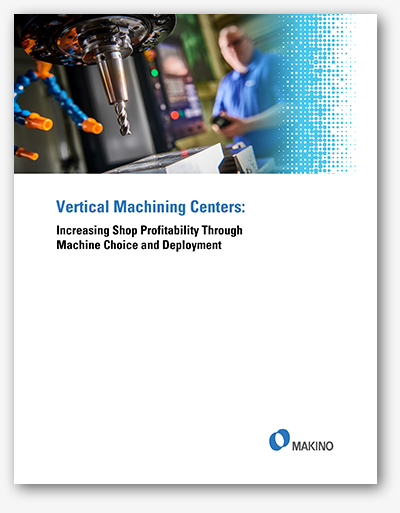.jpg)
If you want to extract the greatest amount of productivity and profitability from your manufacturing operations, it’s important to evaluate how much non-cutting time is occurring when the spindle should be in cut. One of the things that can impact in-cut time is machine technology. Every Vertical Machining Centers (VMCs) offers different technology features that directly affect your machining process and, ultimately, your profitability.
Manufacturers that utilize VMCs and are seeking to increase shop profitability should carefully assess the technical features that impact spindle utilization. This technology—which includes horsepower (hp), torque, and RPM—can either improve or limit productivity and help or hurt the cost per part and profit margins. VMCs with technology designed to maximize spindle utilization can reduce cycle times—resulting in a more profitable operation. By identifying areas of improvement and quantifying the difference they could make in your operations, you can determine whether upgrading to a more productive, efficient VMC is cost effective. Utilizing a highly efficient VMC can result in $350,000 in potential savings over the course of a five-year lease. Plus, with advanced tooling support and greater tool capacity, VMCs can save you as much as $93,750 in parasitic costs per machine.
In this whitepaper, we examine a comprehensive list of VMC production fundamentals you’ll want to assess in order to determine what steps are needed to improve spindle utilization, chip evacuation, and non-parasitic time. This thought-provoking assessment can help you unlock tens- to hundreds-of-thousands in additional profitability over the life of your machine.
>>Download the White Paper>>